CHALLENGES IN MODERN PRODUCT DEVELOPMENT
Efficient production data acquisition for your production with Business Central
The production data acquisition module (PDA) is an indispensable tool for increasing efficiency and productivity in production. With the PDA software, you can optimize the entire production process from planning to execution. By collecting and tracking detailed operational data, you can identify bottlenecks, improve workflows and increase the overall performance of your production facilities.
The PDA module provides a user-friendly interface that enables production employees to manage their tasks efficiently and track progress in real time. From the planning and allocation of work orders to the recording of working times and production errors, the PDA system offers a wide range of functions that enable smooth and transparent production.
The automation of work processes and integration with other systems such as the ERP system simplifies data collection and reduces errors. In addition, the detailed analysis of operating data enables continuous improvement of production processes and better planning of future production steps.
With the PDA module, you can optimize your production processes, increase productivity and strengthen your company's competitiveness.
"Discover how our advanced store floor data collection in combination with Microsoft Business Central can optimize your production processes."

PRODUCTION COST REDUCTION MADE EASY
ENKO BDE integration with Business Central
Seamless integration with Microsoft Business Central makes our PDC the best choice for companies looking to optimize their production and operational processes. You can continue to use the advantages of Business Central and at the same time benefit from extended data entry functions.
THE ADVANTAGES ARE OBVIOUS
INCREASE
MONITORING
IMPROVEMENT
OPTIMIZATION
REFUNDS AND
ANALYSIS
ORIENTATION
This view provides a comprehensive overview of all current production orders. Here you can view important information such as the production order title, the current status, the planned start and end date and other relevant details.
This central overview allows you to track the progress of all production orders at a glance and manage them efficiently.
This overview enables you to track the production process in detail and ensure that all the necessary materials and resources are available on time.
This view enables employees to enter their bookings for manufactured items quickly and easily. Here you can display the different quantities for manufactured, scrap and required items and adjust them if necessary.
The clear presentation and intuitive user interface makes the recording of bookings more efficient, improving productivity and accuracy.
BUSINESS CENTRAL BASIC FUNCTIONS
ORDERS
Production orders for the production of goods.
products to meet material requirements
determine.
RESOURCES-
PLANNING
NEEDS PLANNING
COSTS
CONTROL
and equipment during the
production process.
CONTROL
ADMINISTRATION
production in order to manage material movements and inventories
efficiently.
PLANT-
ADMINISTRATION
SUSTAINABILITY
POSITION AND
ANALYSIS
production, cost structure and efficiency.
You might also be interested in the following:
Get to know the PPS module
Producing with Business Central
Machine data acquisition
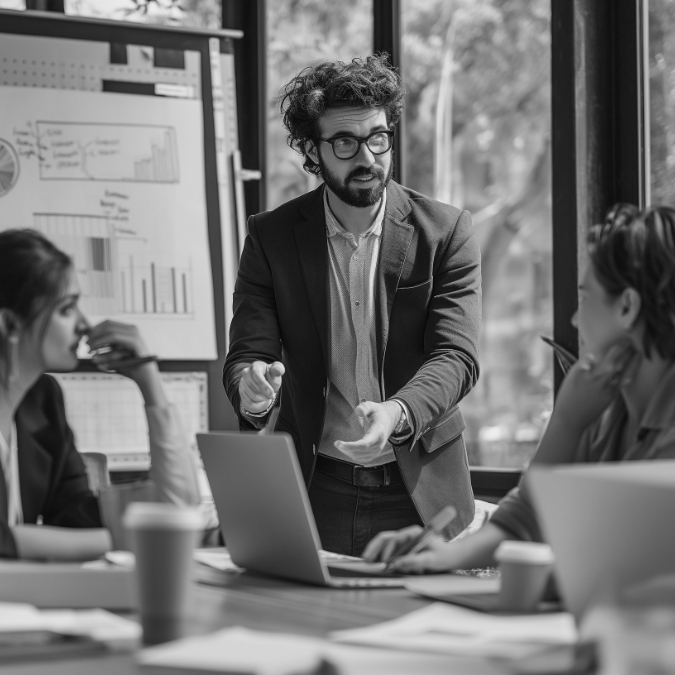
Get in touch with us!
Only a direct exchange reveals what is actually possible. So just give us a call or send us an e-mail. Hopefully we'll get to know each other soon!
ENKO Software GmbH & Co. KG
Dieselstr. 4
DE 54343 Föhren
Telefon: +49 (0) 6502 40491-0
info@enko-software.com